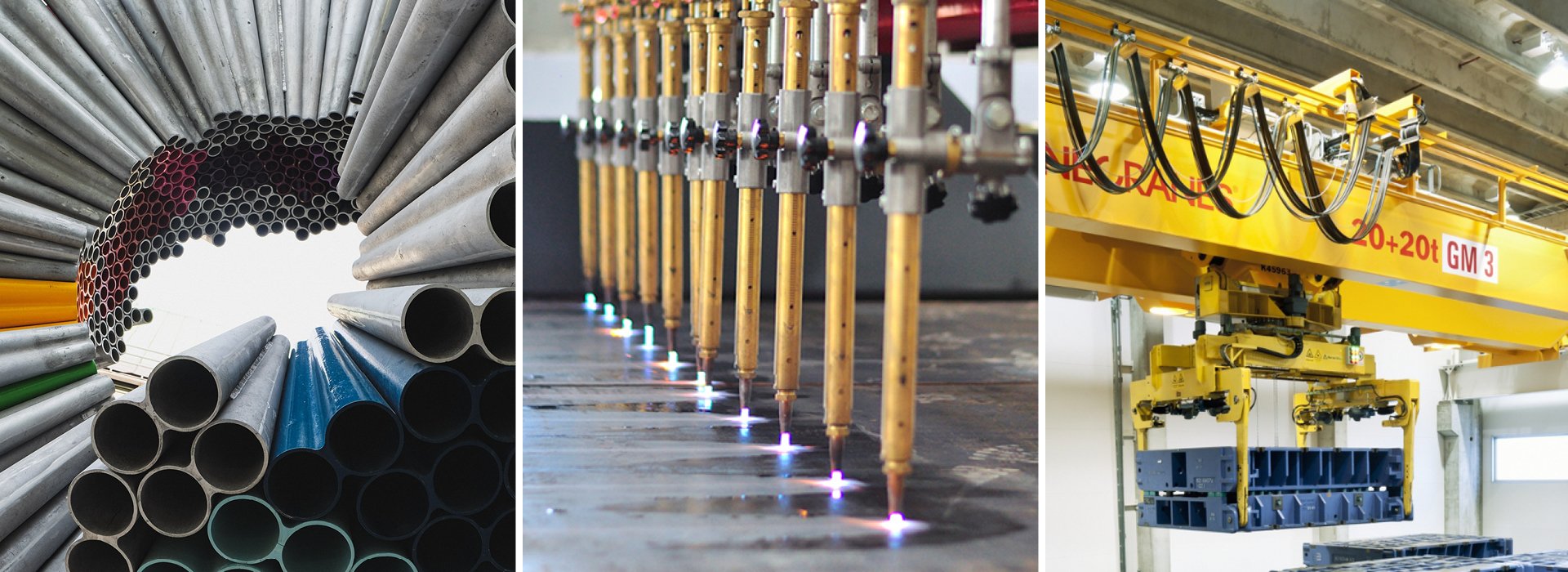
Manufacturing
With a well-trained workforce of over 700 professional staffs, quality management system and a 211k m2 factory, 12,000 MT/month for steel structure, 800 MT/month for cold-formed member and 75k m2/month for steel panel with high technology automatic production facilities, EMG delivers optimal solution, high-quality products and perfect services for your project.Technical design: All of the architectural drawings and structural steel drawings are assessed to ensure safety on the bearing capacity, the load on demand use, environment, art, …
Manufacturing process has three separate stages to manufacture three main constituting components including:
Primary members: Column, Beam
Secondary members: Purlin, Door…
Sheets: Roof sheet, Wall cladding, Flashing…
A. Primary member
1- Cutting:
By the CNC automatic multi-head cutting machine, steel plates can be cut to any shape design. All the plates are cut to any required size by extremely hot temperature with thickness up to 80mm.
2- Hole Punching:
After cutting, use the automatic laminating machine to drill or punch holes on the cutter plates as required.
Equipment and machines: drilling machine, hole-punching machines (03 units).
3- Assembling:
Joining steel plates into I-section building components by automatic assembling machine.
4. Welding and connection details welding:
After assembling, components are transferred to the next procedure of welding two flanges of steel plates with submerged arc weld. This process creates welds with high quality, big intension and absolute sealing.
EMG weld completely by alternating electrical poles welding. All kinds of welds are done in accordance with the latest publish of Vietnamese Technique Manual Book’s standards and instructions.
5. Surface cleaning:
Built-up steel plates and welds are then cleaned physically or cleaned by using the sand-spraying machine, depending on the customers’ choices.
6. Painting :
EMG uses the industrial high-pressure painting machine according to American technology. Building components will be sprayed of grey paint coating or red paint coating or other special paints according to the customers’ choices.
B. Secondary members
1. Forming:
All secondary components such as purlins and girts are manufactured from the Zinc-coated Cold-Rolled Steel Sheet in Coils or black-coated Cold-Rolled Steel Sheet in Coils in accordance with EMG standard. These components are then cold-formed into “Z” or “C” shape with the thickness from 1,5mm to 2,5mm.
The time during adjusting rollers is around 2 ~ 3 minutes without changing rollers. After the roll is formed by this roll forming machine, the surface will be very smooth and beautiful without any scratch on the surface.
2- Hole punching:
Purlins and girts can be supplied plain, or punched using hole punching standard, spaced to your specifications.
3- Painting:
EMG uses the industrial high-pressure painting machine according to American technology. Building components will be sprayed of grey paint coating or red paint coating or other special paints according to the customers’ choices.
C. Panels
All kinds of steel panels are rolled from the high-quality steel, coated cold-rolled steel with undercoat painting conforming to EMG.
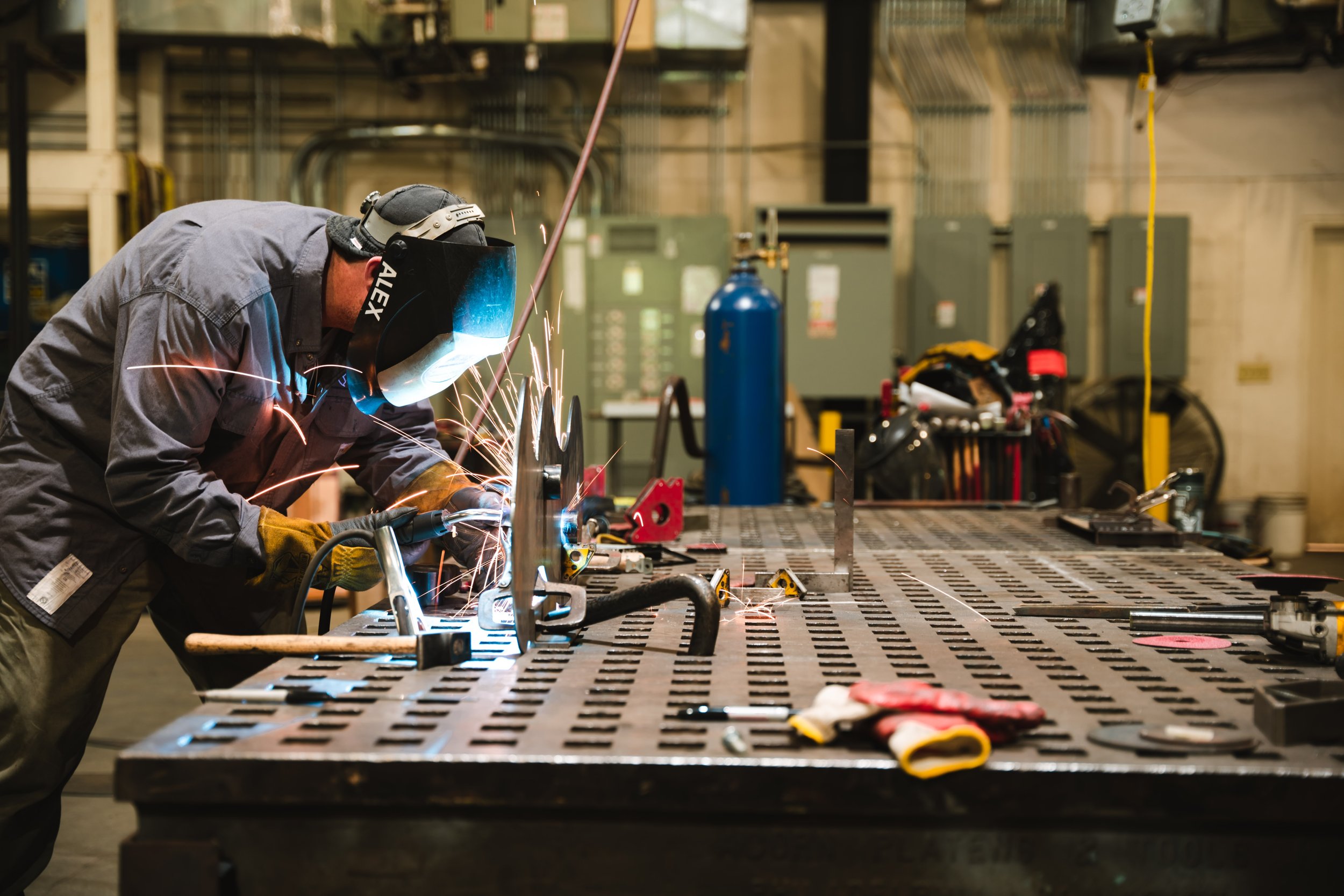
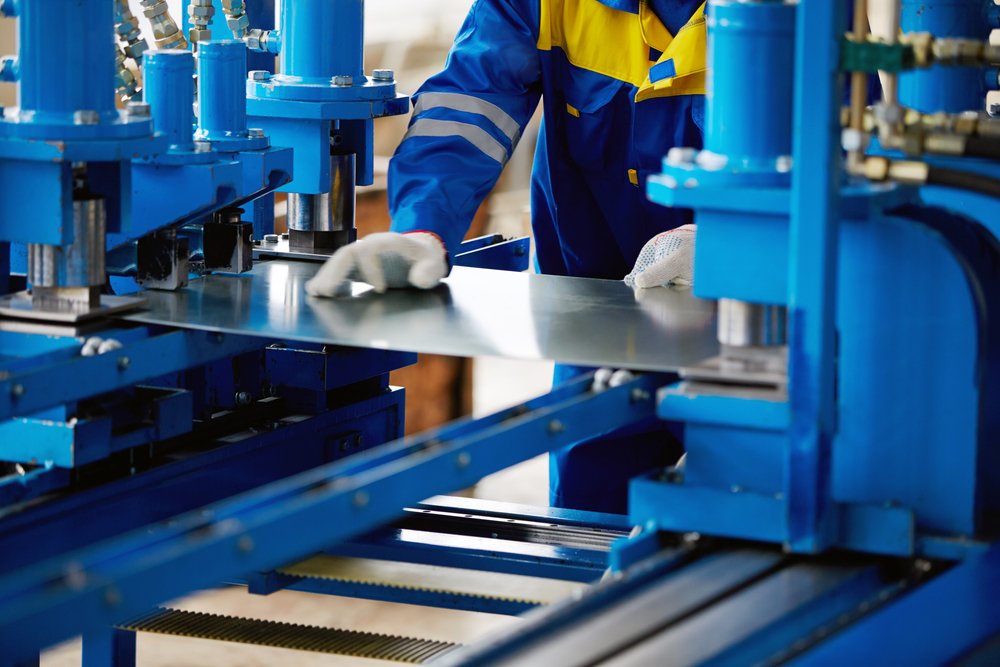